For this particulate project, I was given a complete Simscape model of a 3R robot. My objective was to develop a controller that the manipulator could use to follow a given trajectory.
Once the trajectories of the end effector were developed, I calculated the joint angles for each joint using standard inverse kinematics formulas. For the manipulator control, I used a combination of a PID and a transpose Jacobian controller to control the robot's joint torques. Transpose Jacobian control is a popular method of controlling robotic systems and is less computationally intense than inverse Jacobian. The Simulink block diagram of the controller is shown in the image below.
Internship Experience
SARTORIUS STEDIM (Jun 2018 - Aug 2019) - Product Development Intern
DENTSPLY SIRONA (May 2016 - Jan 2017) - R&D Intern
I had the privilege of interning at the R&D departments for two biomedical device companies over a span of three years. I got to advance product development for a line of dental devices, as well as biopharmaceutical storage containers.
My projects mostly involved mechanical testing, machine & CAD design, as well as general troubleshooting. Although I learned a lot from each company, rapid prototyping became my most valuable skill. I learned how to apply concepts of machine design to create mechanical devices fit for product testing and development. I have a working experience with pneumatic and electric actuators, joint and linkage designs on machinery, proficiency with machining my own parts, and CAD knowledge to design everything together.
Here is an example of one of the projects I worked on at Sartorius.
Pallet Restraint Mechanism
For this project, my goal was to design a mechanism which would restrain a pallet carrying a large load of products (<1000 lbs). The obvious requirement was to prevent the pallet from moving in any direction. The mechanism also had to be easy to use and quick to operate. CAD models were made in PTC Creo 4.0, and the assembly is shown on the right.


The table above shows the design constraints as well as the actions I took to overcome them. The image on the left shows another angle of the mechanism in CAD. I tested the mechanism myself by 3D printing the driver and driven links and actuating the cylinders in the video on the right. After showing off the proof-of-concept, the links were machined from a local shop. The finished mechanism worked well at restraining company pallets, and was quick and simple to operate as intended from the start.

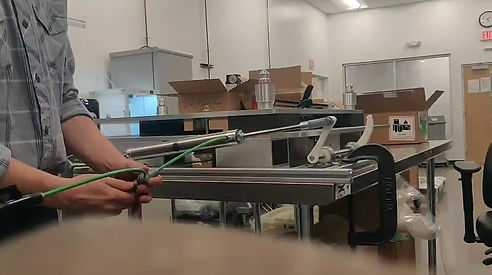